What tax changes will affect manufacturers in 2024?
What does the factory of the future look like? Embedded technology and the availability of data are enabling Industry 4.0, a high-tech fourth industrial revolution. But a worker shortage is still impacting operations, influencing companies to reimagine the way people work and consider reskilling their current employees. And companies are finding ways to mitigate the effects of supply chain disruptions caused by strikes, layoffs, geopolitical events, and extreme weather. And of course, industry changes beget tax changes (and sometimes vice versa).
The digitalization of manufacturing
Like many industries, the manufacturing industry is turning to technology to stay competitive and overcome challenges. While it’s tempting to imagine a bunch of Roseys from “The Jetsons” or Benders from “Futurama” assembling cars and operating machine presses, the approach is more high tech than high mech.
According to the Deloitte 2023 manufacturing industry outlook, 62% of manufacturers surveyed are investing in robotics and automation to speed manufacturing, reduce costs, and alleviate pain caused by labor shortages; 60% are looking to data analytics to improve forecasting and spot supply chain shortages before they affect production; and 39% are using the Internet of Things (IoT) to collect and analyze data from sensors on the factory floor and embedded in industrial equipment to improve manufacturing, supply chain training, and product maintenance.
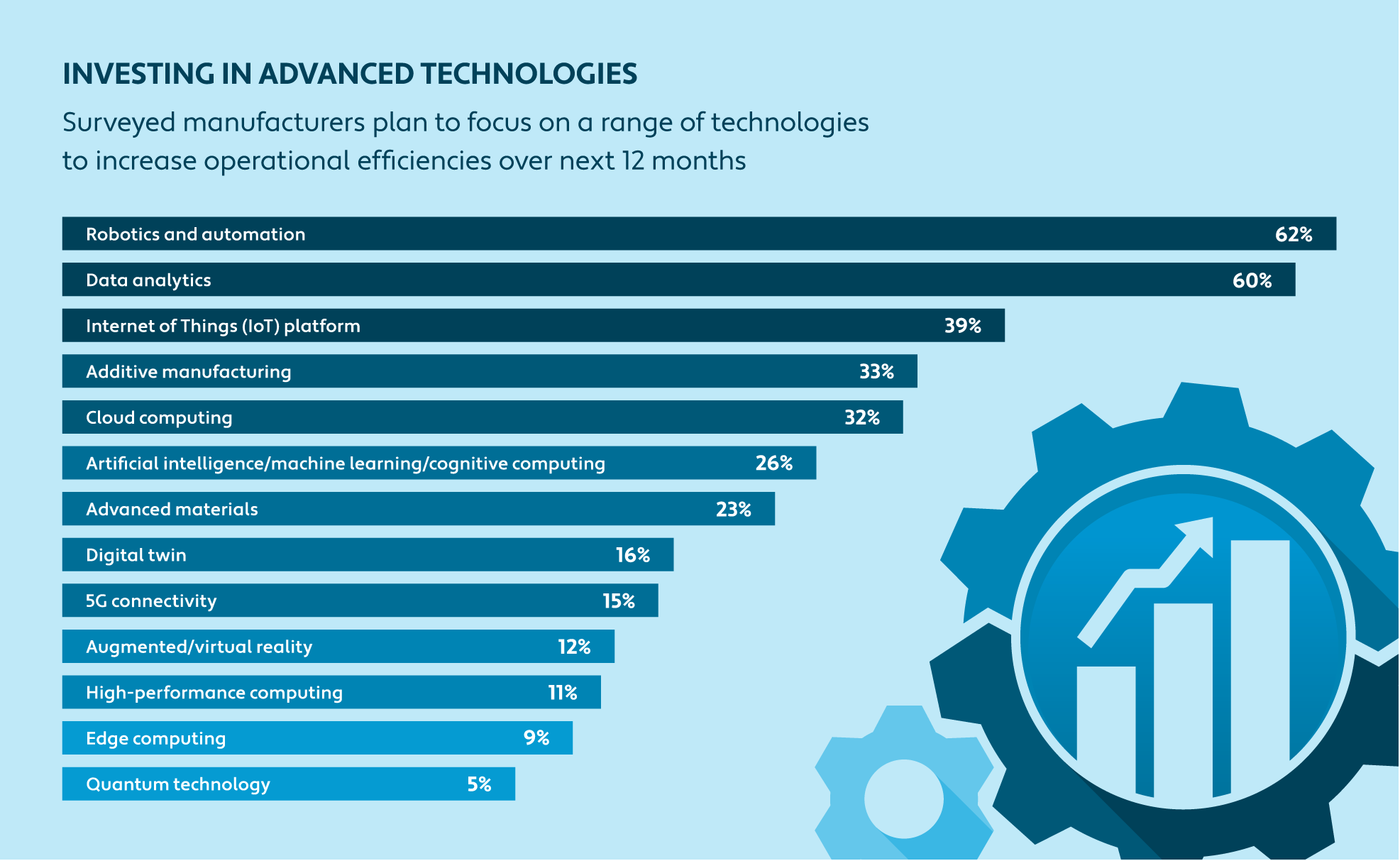
SOURCE: Deloitte
Of those surveyed by Panorama Consulting Group in 2020, manufacturers were also the main users of ERP systems at 33.66%. In fact, according to respondents of an Avalara and IndustryWeek survey, a big tax compliance priority for manufacturers is for their technology to integrate with existing ERPs and other systems.
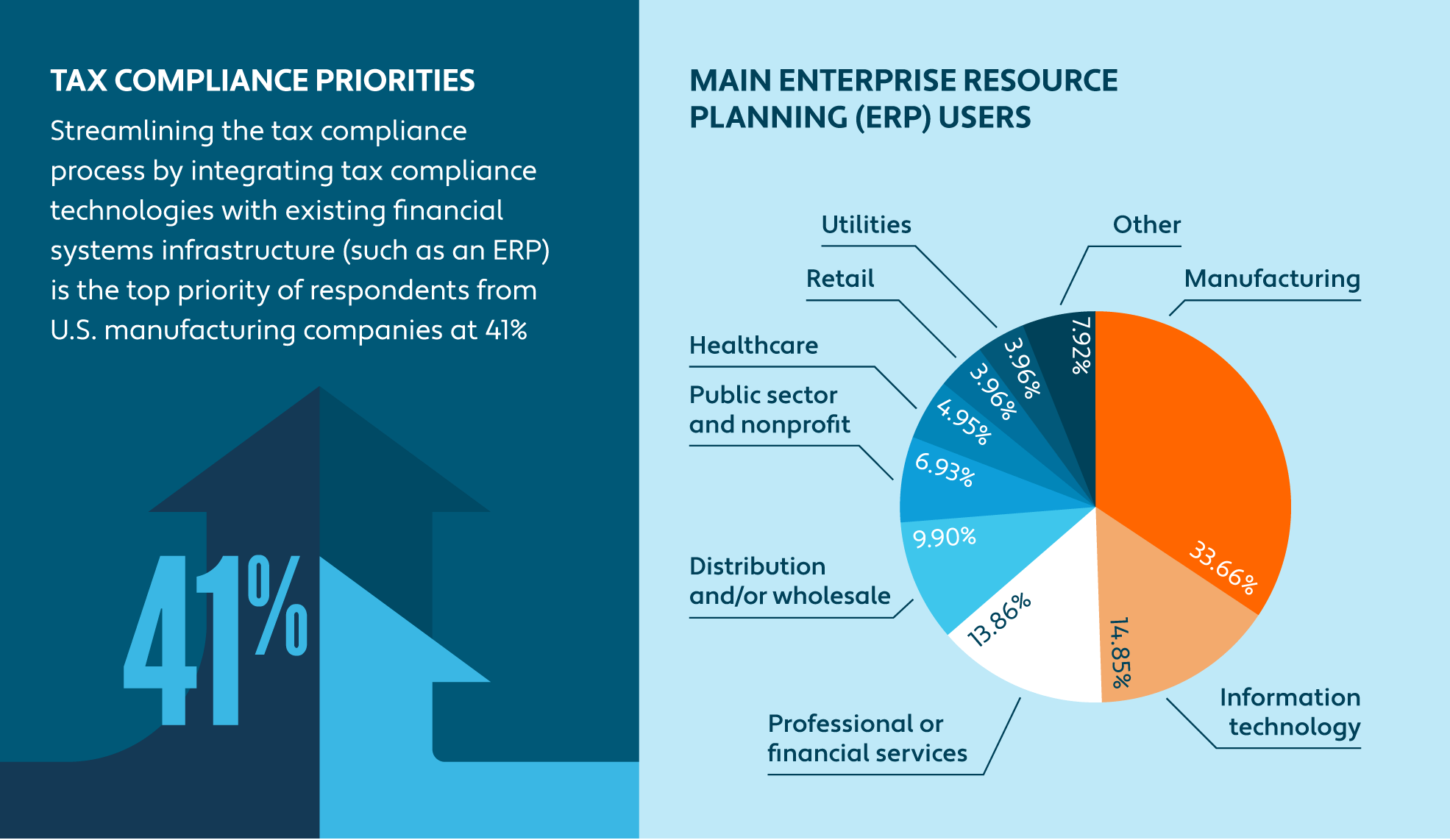
SOURCE: Avalara, Panorama Consulting Group
Research found that those manufacturers who have adopted emerging technology are more agile than those who have not; they are able to pivot if the industry calls for a change, and they have increased supply chain visibility and can better adapt to supply chain challenges (something we have become acutely aware of in the last few years).
The industrial revolution goes high tech: Industry 4.0
Are technological advancements in manufacturing ushering in another industrial revolution? While previous revolutions in manufacturing have been characterized by steam, electricity, and computers, the era we’re currently experiencing is all about smart technology. Industry 4.0 (the high tech-sounding name for the fourth industrial revolution) is driven by the Internet of Things, cloud computing, artificial intelligence and machine learning, edge computing, cybersecurity, and digital twins.
The microfactory: Smaller and better than ever?
Maybe bigger isn’t always better when it comes to manufacturing. Integrated technology and digital transformation have created the perfect opportunity for the resurgence of the microfactory, a small, modular, technologically advanced manufacturing facility. These structures can be set up near customers to reduce shipping and storage costs.
Factory simulators: Digital twins
What if you could put those hours spent playing RollerCoaster Tycoon, Factorio, or any number of logistics and resource management video games to good use? Some manufacturers have started using digital twins — virtual models of a physical object — to revolutionize operations. Smart factories are equipped with sensors that relay data and performance insights, and the virtual model can be used to run simulations, test out new processes, and study performance issues before solutions are applied to the physical factory.
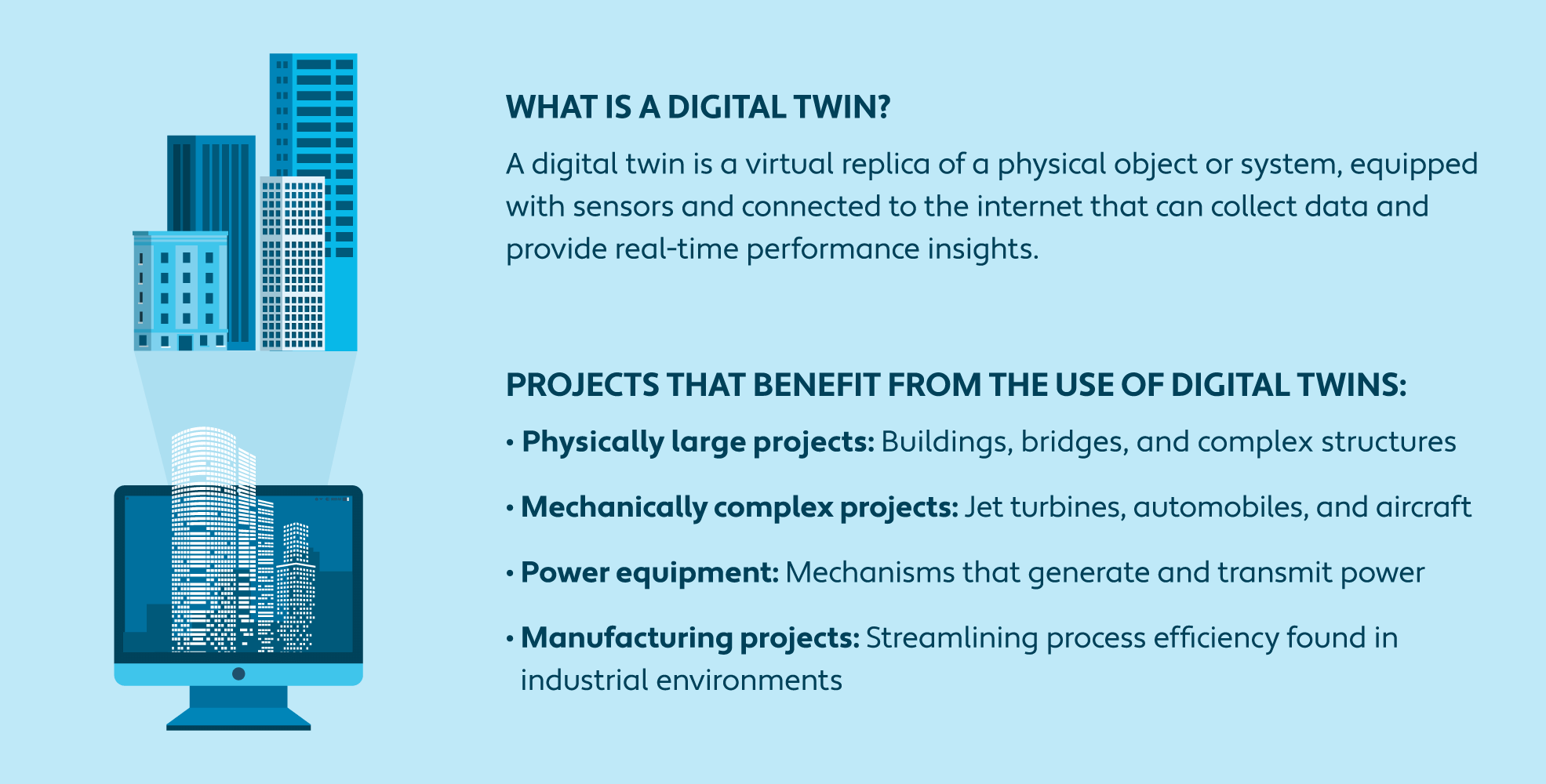
SOURCE: IBM
Artificial Intelligence for real-life results
From writing high school term papers to imagining a full landscape behind the “Mona Lisa,” people are using artificial intelligence (AI) everywhere. So how are manufacturers making it work for them? AI’s ability to analyze huge amounts of data can come in handy when Industrial Internet of Things (IIoT) sensors are collecting and sending data from machines and equipment, making it easier to identify trends and catch problems earlier.
Speaking of catching problems earlier, wouldn’t it be nice to know ahead of time — based on real-time data — when a belt should be changed or a die needs to be sharpened? AI can help manufacturers put predictive maintenance systems in place and proactively address workplace safety hazards.
Tax officials have also started relying on AI and other new technology to uncover noncompliant businesses. Experts in data science and tax enforcement have partnered to apply machine-learning technology to identify areas of potential compliance risk. Similarly, businesses can use the same type of technology to help ensure they remain in compliance and competitive. An increasing number of businesses are turning to tax automation software to reduce the burden of managing sales tax and exemption certificates on their own. More on that later.
The new age of manufacturing employees
Even though the digitalization of the industry is changing the types of skills needed in manufacturing, workers are still needed — and businesses are finding good help hard to come by. According to the 2023 Manufacturing Industry Outlook, there was a record high of roughly 800,000 unfilled manufacturing jobs across the U.S. in 2022.
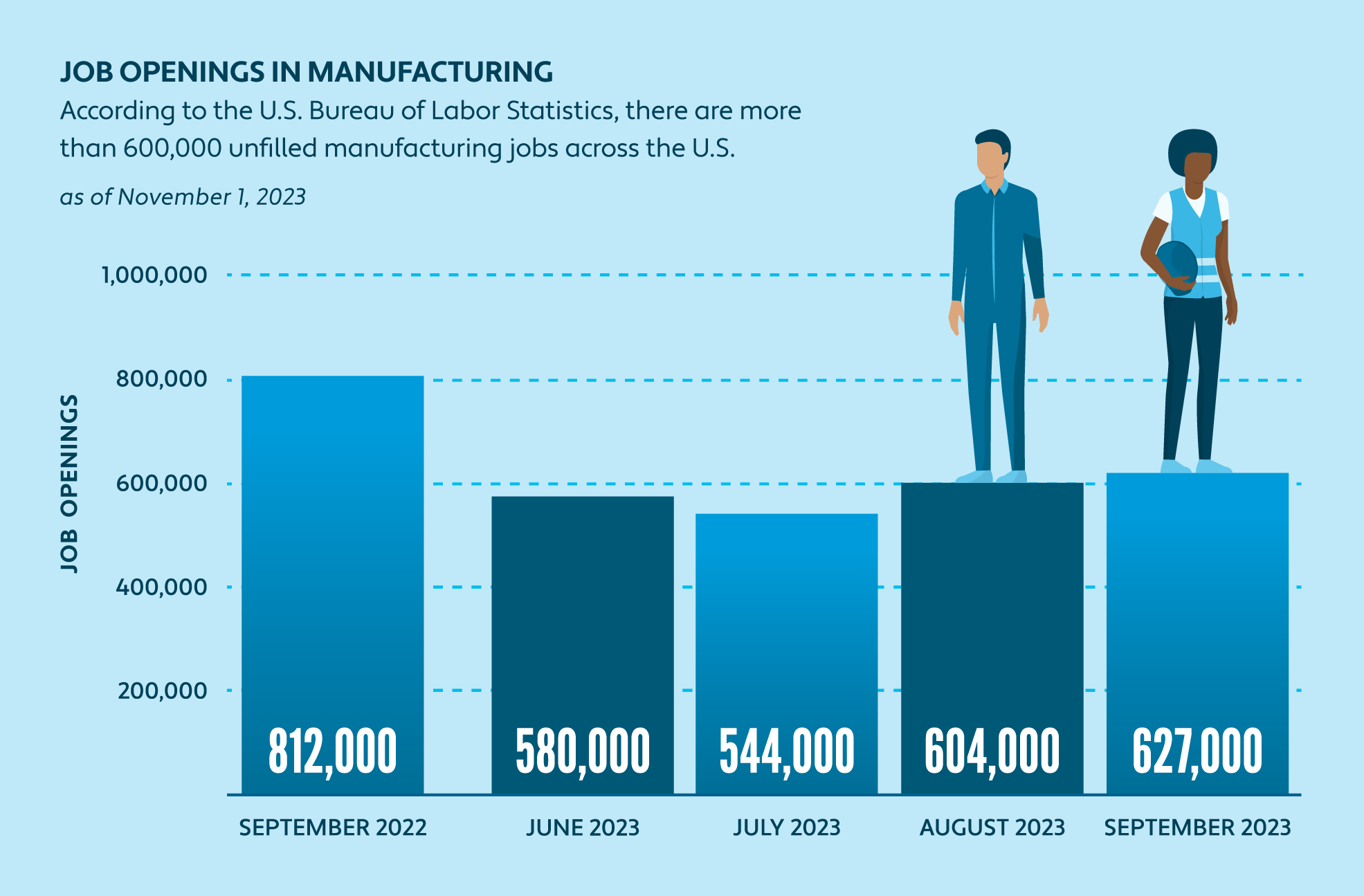
SOURCE: BLS
Employee attraction and retention in manufacturing
Attracting and retaining talent will remain a top priority for many manufacturers in the next year. Manufacturers are considering raising wages; investing in startups or collaborating with academic ecosystems to gain access to new technology and talent; focusing on diversity, equity, and inclusion initiatives to attract more women and racially and ethnically diverse workers to the industry; and exploring ways to make the workplace more flexible. Another way manufacturers can address the labor shortage and prepare to meet the changing skills needs of the industry is by upskilling their current workforce and giving employees the technical and digital training needed to work with new systems.
Keeping manufacturing close to home
There’s no place like home. At least that’s what many manufacturers are finding as it relates to reshoring their operations. The Biden administration is rewarding manufacturers that keep operations in the United States too; the Inflation Reduction Act establishes tax incentives and policies for businesses to manufacture in the United States, the CHIPS and Science Act sets aside $50 billion for the domestic semiconductor industry, and the Infrastructure Investment and Jobs Act allocates $1.2 trillion for transportation and infrastructure.
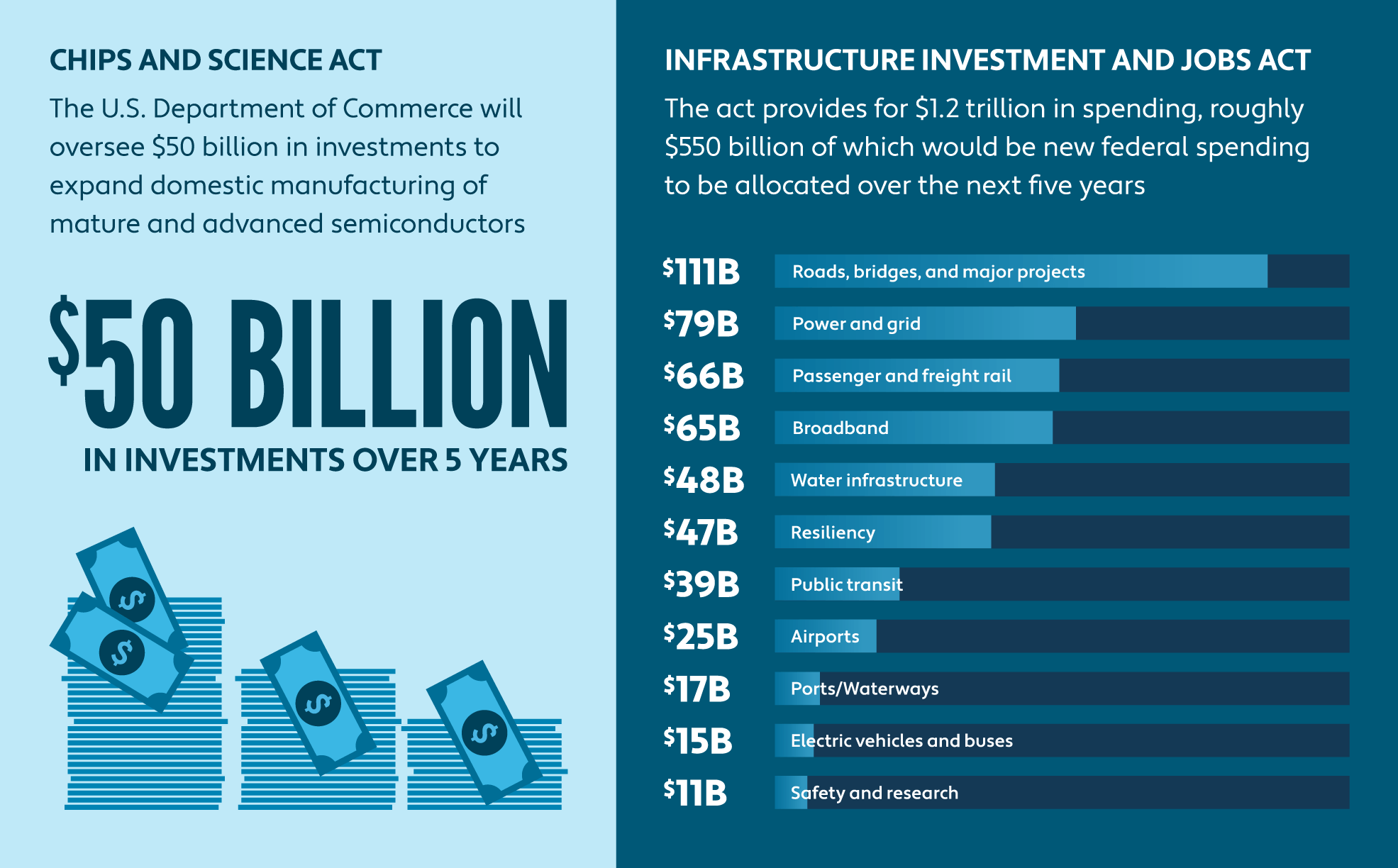
SOURCE: McKinsey & Company, EY
Then there’s the added benefit of being that much closer to your suppliers. According to recent supply chain research, 80% of surveyed manufacturing executives experienced a “heavy” to “very heavy” impact of disruption on their supply chains over the last year and a half. So executives hoping to mitigate supply chain disruptions, reduce transportation costs, and increase flexibility may consider doing some domestic real estate shopping.
Will supply chain issues continue in 2024?
It’s hard to remember a world before constant supply chain issues, and it doesn’t look like they’ll be in the rear view any time soon. While it seems like the supply chain is stabilizing after a tumultuous few years (there’s only been a 3% increase in disruptions over 2022), disruptions are still happening. Between January and June 2023, supply chain risk management platform Resilinc recorded 8,197 supply chain disruptions, such as shutdowns, production halts, warnings/citations, and labor accidents. According to a study from McKinsey, companies across industries can expect a supply chain disruption that lasts a month or longer to occur about every four years.
One of the biggest factors behind supply chain delays and issues is labor disruptions like strikes and layoffs. In the first two weeks of the six-week-long United Auto Workers strike across Ford, General Motors, and Stellantis plants, the auto industry lost over $3.9 billion, according to Michigan-based consulting firm Anderson Economic Group.
The effects of geopolitical unrest continue to ripple and disrupt supply chains. Fuel prices soared in 2022 after Russia’s invasion of Ukraine, for example. And while prices have leveled out in the year or so since, crude oil prices are predicted to rise in 2024. More frequent and severe weather events are also disrupting supply chains. Wildfires, hurricanes, and even higher- or lower-than-usual temperatures impact ports, highways, and factories worldwide.
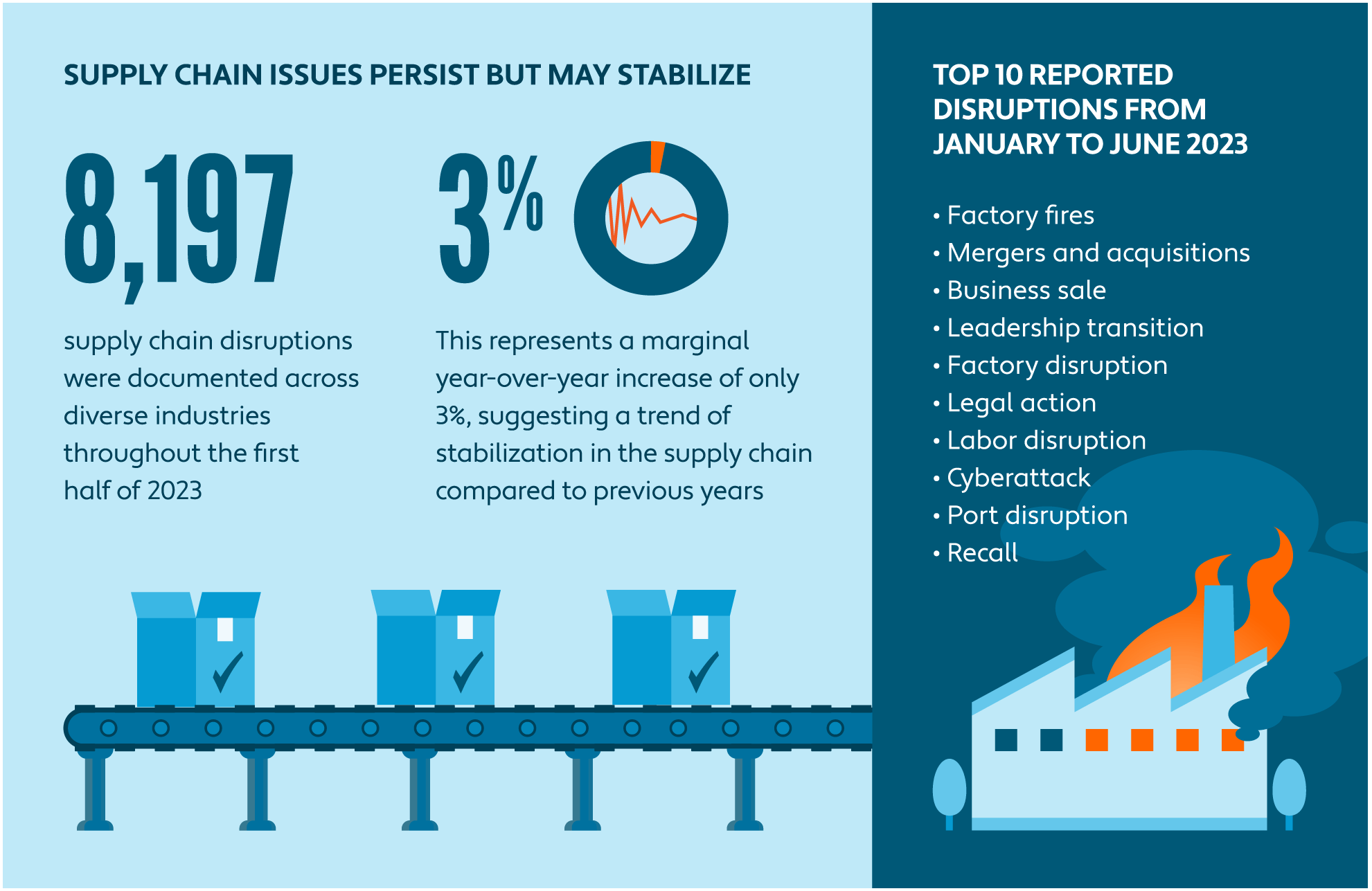
SOURCE: GlobeNewswire
The supply chain goes digital
If the rest of the factory is going high tech, shouldn’t the supply chain too? A digital supply chain uses integrated technology to give stakeholders and participants near-real-time insights about what’s happening at every step of the chain. Stakeholders have more visibility into supplier performance and customer needs, which allows them to spot potential problems earlier in the process. Oracle NetSuite suggests a digital supply chain can increase on-time delivery to customers by 8% and reduce costs by up to 50%.
It also might be able to better predict customer demand. As companies and consumers adjust to life after the pandemic, we’re finding out which trends are here to stay (remote work, our love for sourdough bread) and which are falling by the wayside (remember “Tiger King”?). Estimating wrong can be costly; Peloton built a factory to produce more bikes after demand exploded during 2020 and 2021. It completely misjudged what its market would be when gyms and fitness centers reopened.
Drop shipping trends
Some companies are opting to save costs on warehouses and taking a new approach to customer order fulfillment: drop shipping. When a seller takes an order from a buyer, the seller orders that item from a supplier, who ships it directly to the customer on behalf of the seller. But because the transaction involves multiple companies, multiple transactions, and often a few states, it can complicate sales tax.
Introducing product as a service
Some car manufacturers are finding opportunity in offering their product as a service. Volvo and Porsche, for instance, are giving customers usage of cars for an enrollment fee and monthly subscription. This gives drivers access to a car without the commitment of a lease or the costs and responsibility of registration and maintenance, and it gives manufacturers consistent revenue streams and offers more predictable demand. Plus, manufacturers can get insight into how customers are using their products.
Manufacturers can also get in on the XaaS (anything as a service) model with servitization, or providing services like maintenance, repair, and upgrades after the original sale is made. Offering services in lieu of or in addition to selling products can complicate taxability for a business. Each state has different rules and regulations for how services are taxed, and businesses might find themselves subject to use taxes where they only had to worry about sales tax previously. And if you’re adding a recurring billing or subscription sales model, your business has that many more chances in a year to get sales tax right.
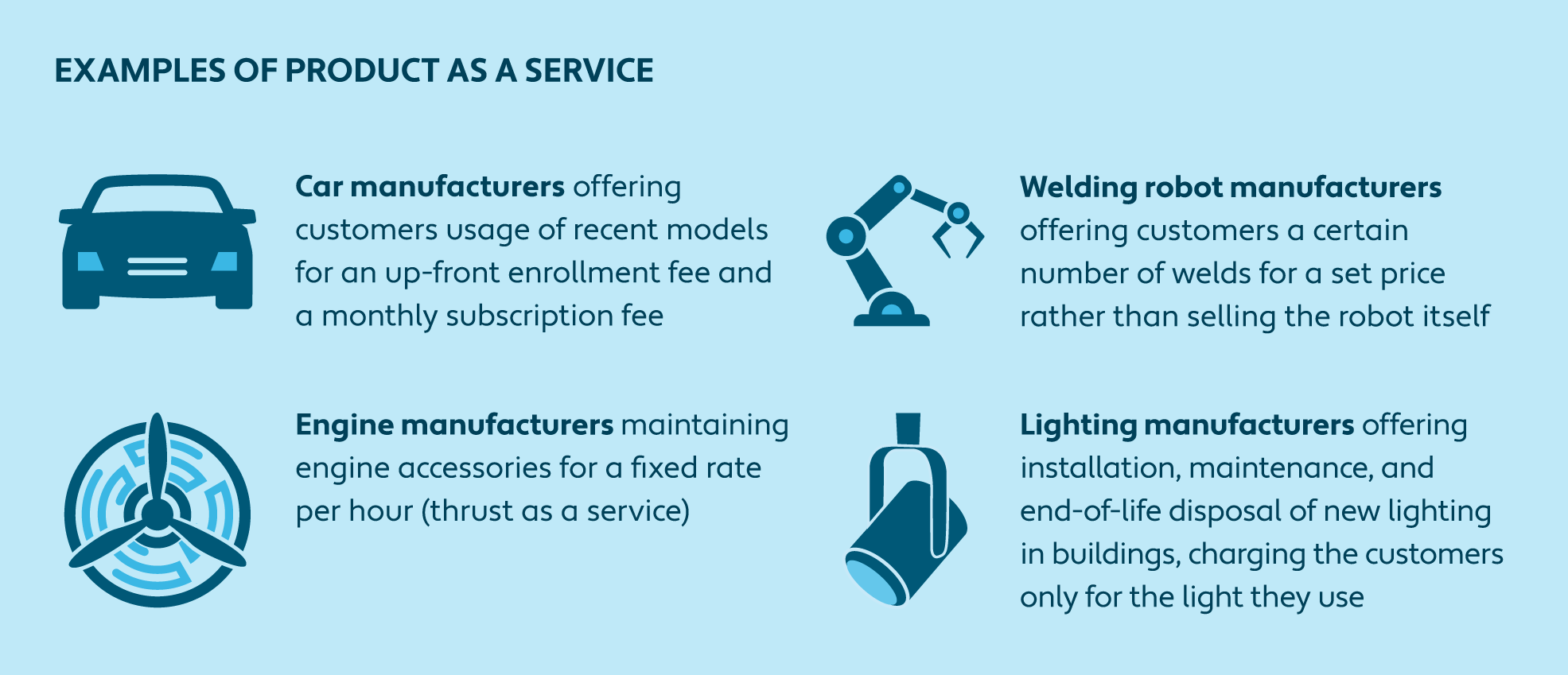
SOURCE: Oracle (1), Oracle (2)
How manufacturing trends affect sales tax nexus
While businesses in every industry deal with expanding tax obligations based on nexus, those in the manufacturing sector face unique challenges.
In order to stay agile and mitigate the effects of supply chain disruptions, manufacturers have been reshoring their operations and broadening their vendor lists. But having inventory or operations in more places subjects them to physical nexus. And while a remote workforce may enable businesses to attract much-needed talent, having employees across a number of states can trigger tax obligations.
Even adding services to your list of offerings for your customers could change the way your business is taxed. When you add in that each state has different, ever-changing rules and regulations for how products and services are taxed, tax compliance can get complicated quickly. Indeed, keeping up with changing tax laws and guidelines is the number one tax compliance headache for 54% of manufacturers that responded to a 2022 survey.
Economic nexus, the triggering of a sales tax obligation based on business activity in a state, also continues to be a challenge for manufacturers. This is especially true when manufacturers can and do sell directly to vendors. If you have nexus with the state where your vendor is located, you’ll need to collect and remit the applicable sales tax or a valid exemption certificate at the point of sale.
Economic nexus can also impact a manufacturer’s purchases. If you buy supplies from a vendor with nexus, you’ll need to pay sales tax or provide the vendor with a valid exemption certificate. If the vendor doesn’t have nexus, you may be responsible for remitting use tax directly to your state tax authority.
Exemption certificate challenges
Even tax-exempt businesses aren’t excluded from the complexity of compliance. Many states include exempt sales of products or services in their economic nexus thresholds, so it’s imperative to monitor sales into each state and register to collect and remit tax when sales reach the nexus threshold.
Not having the right paperwork on file at the time of sale can be costly. In March 2023, the District of Columbia Court of Appeals held that exemption certificate data provided after the time of sale is invalid when a D.C.-area hospital sought a sales tax refund of approximately $1 million on taxes paid on prepared meals for resale. But since the hospital failed to provide the required resale certificate at the time of purchase, it was ruled that they were not eligible for a refund.
Whether your business is an exempt buyer or seller of exempt products, you’re going to need the documentation to back it up. Manufacturers often have to deal with hundreds or even thousands of exemption certificates, and there’s a lot of room for error if your team is manually collecting, verifying, and storing them. Missing exemption certificates can be an issue during state audits, and can result in significant penalties.
Some companies are turning to artificial intelligence to manage sales tax and exemption certificates. Not only does automation software take the burden of compliance off businesses, but those software providers are using AI to power their own solutions. Avalara, for example, uses built-in machine learning to validate exemption certificates stored for customers.
“Artificial intelligence holds great promise when it comes to dramatically reducing the time it takes to do routine tax compliance tasks,” says Kael Kelly, Avalara General Manager of Certificates and Tax Research. “For instance, Avalara uses machine learning in our software to assist in validating exemption certificates. We also believe customers will soon be able to use generative chat to help research tax rates and laws.”
Kelly is optimistic about the future of AI in compliance: “In the future, AI could not only automate high-volume tasks, it could potentially recommend ways to improve workflows, prioritize work, and increase compliance at a lower cost.”
New sales channels, new problems
Many manufacturing companies are making changes to the way they sell by adopting new sales channels. There are advantages to selling directly to customers and through marketplaces — it allows you to reach more customers and accelerate growth. But as your customer base grows, so can your tax obligations. You need a system in place to track nexus thresholds and easily register to collect and remit tax in new jurisdictions.
B2B marketplaces have unique compliance laws
Businesses selling through an online marketplace should be aware of the laws and regulations for marketplace facilitators and sellers. Some marketplaces are required to collect sales tax on behalf of sellers, and some aren’t. Brush up on your marketplace facilitator knowledge before you make a costly mistake.
In addition to dealing with economic nexus and marketplace facilitator laws like their business-to-consumer (B2C) counterparts, B2B marketplaces must validate exempt sales by collecting and maintaining exemption certificates for each and every third-party seller. They must also properly validate, document, and report both taxable and exempt sales. It’s an enormously burdensome task.
Cross-border growth
Cross-border ecommerce is growing. In fact 64% of manufacturers, retailers, and logistics service providers surveyed either conduct cross-border ecommerce or plan to within the next year. But new frontiers often mean new challenges, like delayed shipments, customs compliance, supply chain costs, as well as tariffs and duties.
E-invoicing mandates are becoming popular globally, and while they’re not yet required in the U.S., manufacturers buying or selling internationally will want to become familiar with electronic invoicing processes.
This time, it’s personal: Property tax issues for manufacturers
According to a recent market research study, 56% of enterprise companies surveyed receive between 500 to 10,000 property tax bills each year. Each of these bills must be received, tracked, responded to, and paid. And for small businesses without a dedicated tax team, that can mean a lot of time spent on non-revenue-generating business. Every state has its own rules and regulations when it comes to property tax, and those rules are continually evolving.
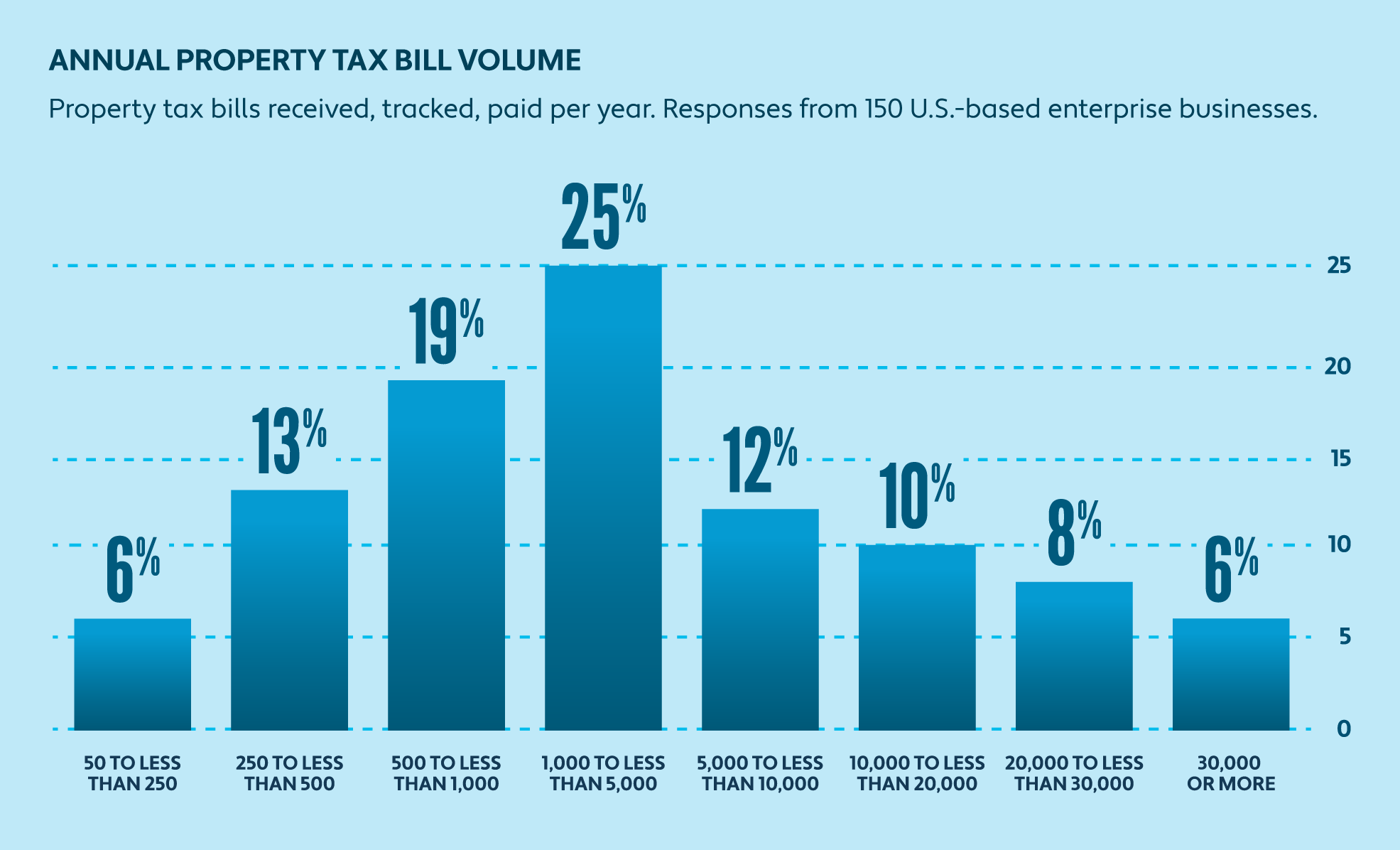
SOURCE: Avalara/Potentiate survey
Property tax isn’t just real estate. Personal property tax includes things like office supplies, machinery and equipment, and even vehicles. Not every state taxes business personal property, however. So if you’re planning on building a new warehouse or factory, the location can make a big impact on what your tax bill looks like.
Tax compliance for both real and personal property can get complicated quickly. If your team is managing it manually, you could be losing valuable time and money, and opening yourself up to costly mistakes.
Environmental fees
According to the U.S. Environmental Protection Agency, the manufacturing and raw materials industries were responsible for 23% of greenhouse gas emissions in the U.S. in 2021. To combat the environmental effects of eco-unfriendly activities, a number of states have started imposing environmental fees on companies that use or create materials like hazardous waste or lead-acid batteries.
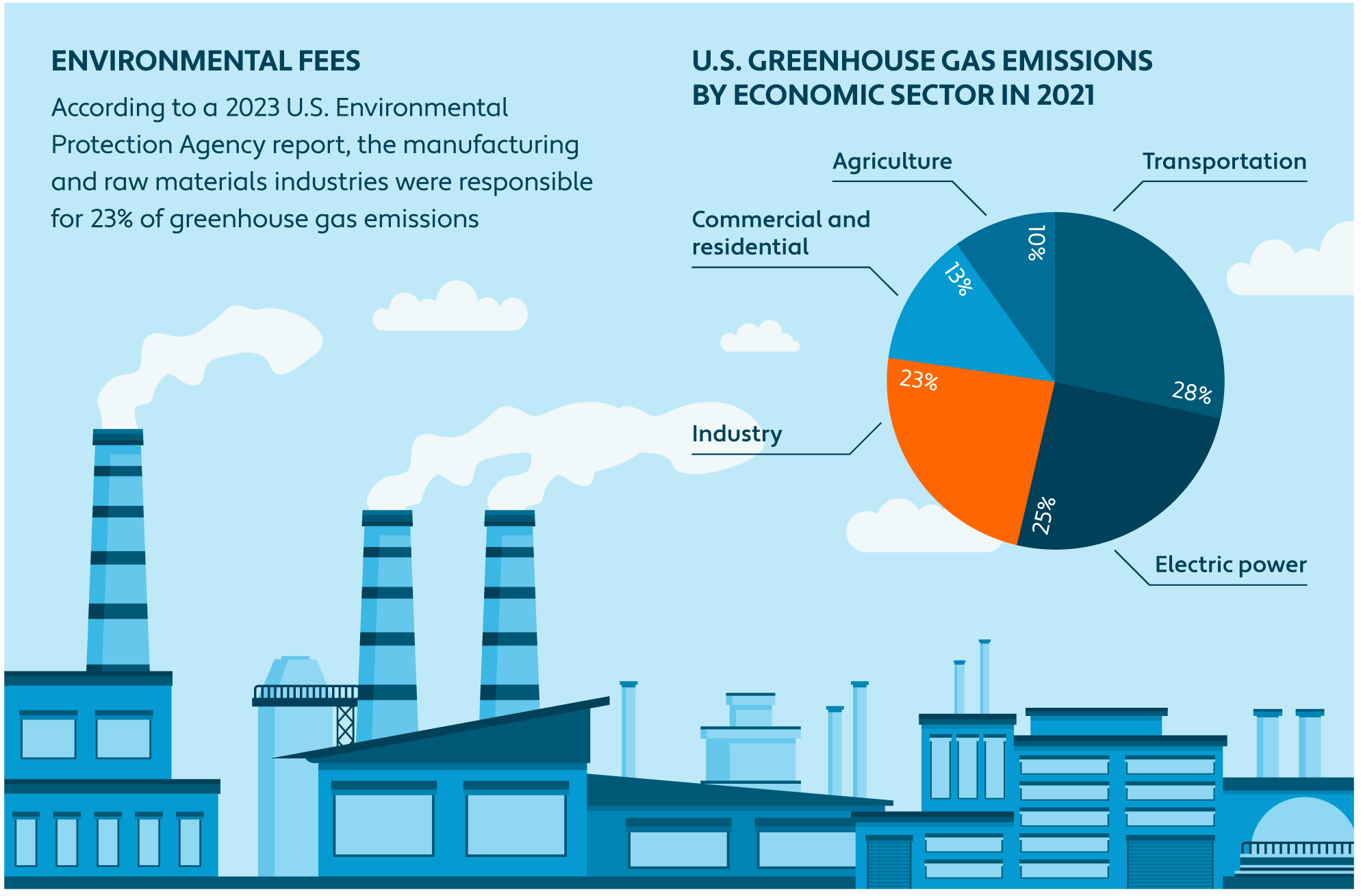
SOURCE: EPA
Since these types of fees don’t typically fall inside a tax department’s normal purview, it can be challenging to stay on top of them. Tax or finance departments may not know about the applicable fees until well after they take effect, or if they do know about them, they may not have the information needed to comply with the fees.
If your company, like many, tends to operate in silos, it might be time for some cross-departmental collaboration.
Sustainability
It’s not just fees that are driving companies to be more environmentally conscious — consumers and corporate purchasers are increasingly considering carbon footprint when they make buying or investment decisions. Thus, manufacturers are incentivized to use less water, reduce waste, and commit to other sustainable practices.
With all these changes and trends, it sure looks like businesses in the manufacturing industry are in for an interesting year. But not to worry — Avalara will be right there with you, keeping track of tax changes and helping you understand how they might affect your business.
How Avalara can help
Avalara Exemption Certificate Management allows manufacturers to collect, store, and manage their exemption certificates, making it easier to stay tax-compliant and audit-ready. Coupled with Avalara AvaTax, it can also monitor for potential sales tax obligations and collect the certificates you need from customers in new states.